Before we get into the 3 lessons, let’s take a moment to define what Supplier Collaboration means in the context of this post. After all, Supplier Collaboration is one of the broadest terms in industry today. When it comes to manufacturers that I speak with, including those referenced below, Supplier Collaboration focuses on the process of aligning contract, outsourced and component manufacturers with R&D, Procurement, and others to deliver on key goals and drive innovation. To do this, companies need a supplier collaboration solution that reduces errors, scrap, rework; improves supplier quality; minimizes wasted engineering time; and improves delivery accuracy. This leads to the first thing I learned at PTC/USER.
Engineering teams have less time for innovation because they have become the human-powered supplier collaboration portal, spending 50% of their time finding, packaging, sharing and explaining technical data.
Lesson 1: Manufacturers know what they want in a supplier collaboration portal, but are struggling to achieve their vision. During my presentation at the event, I asked the audience what would be on their wish list for a supplier collaboration solution that drives innovation. They shared a lot of ideas, collected in the graphic below. And we rearranged their ideas into the following requirements that everyone agreed on:
- Simple, real-time communication tools that are time-limited, access controlled, and fully traceable
- Simple, secure file-less content sharing that is time-limited, access controlled and always up to date
- Data that is synchronized with authoritative source revision control and workflows
- Markup tools that everyone can use to markup up all types of 2D and 3D data, not just documents
Everyone agreed on these core elements that would result in a redefined supplier collaboration solution. But why is it important and how do you get there? That’s what lesson 2 and 3 cover so read on.
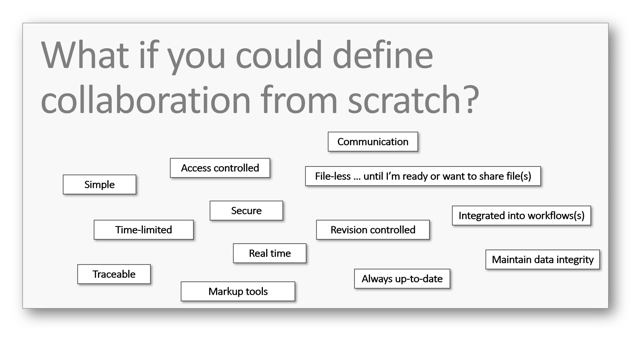
Lesson 2: Engineering teams (procurement, and suppliers) have less time for innovation because they have become the human-powered supplier collaboration portal. Recent research from Lifecycle Insights reported that 50% of engineering time is spent finding, packaging, sharing and explaining technical data. I was surprised by this number when I first saw it, but everyone I spoke with at PTC/USER confirmed this; engineers spend far too much time manually carrying out tasks to support collaboration with procurement and suppliers. For most companies, engineers themselves are the supplier collaboration portal for product development and NPI because existing tools don’t support technical data collaboration. Most supplier collaboration tools focus on supplier registration, execution, forecast/schedule management, and other transactional supplier interactions. This leaves a significant collaboration gap between engineering, procurement and suppliers that is filled by non-secure file sharing apps, static screenshots, email attachments, and untraceable conversations that are completely disconnected from PDM/PLM or ERP. Engineering wastes precious cycle time filling the gap without reducing error rates. Supplier costs increase to cover the gap through bid inflation, scrap, and rework. And Procurement is stuck in the gap focused on supplier schedules and transactions rather than innovation and quality.
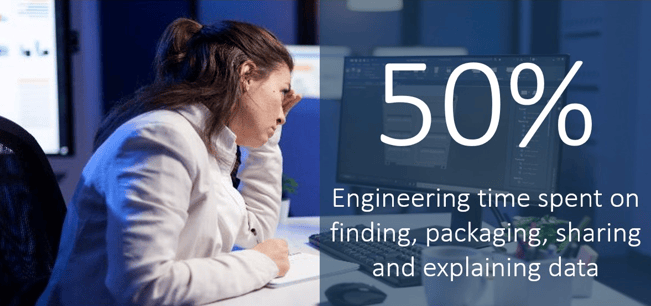
This must be the part of the post where we learn how to solve these challenges. Well, I have good news and bad news, which do you want first? Let’s start with the bad news.
Lesson 3: There is confusion about what PLM natively offers, what it will offer, and how supplier collaboration gaps can be filled. The problem is understood, the need is recognized, but the path to a solution is unclear. Many people I spoke with felt like they should be able to solve these challenges with the tools they have, but it turns out that engineering, procurement and suppliers continue to gravitate to file sharing and communication apps for supplier collaboration. File sharing apps make it easy to share and access content, and communication apps make it easy to exchange messages and send content. PLM offers structured authoritative data, configuration and change management throughout the product lifecycle, but struggles to displace file-sharing apps, and email/chat tools. This once again leaves gaps as companies compromise collaboration.
Supplier Collaboration: The process of aligning contract, outsourced and component manufacturers with R&D, Procurement, and others to deliver on key goals and drive innovation.
The good news: Anark’s supplier collaboration solution fills those gaps by tightly integrating with the major PDM/PLM platforms, including Windchill. This extends Windchill and it’s powerful PLM capabilities to the supply chain with automation services that eliminate the “human-powered portal” and a mobile-first collaboration experience that eliminates untraceable file-sharing and email-based collaboration. The confusion is gone. Errors, scrap and rework are reduced. Engineering, procurement and suppliers collaborate together in one place, and everyone innovates faster.
For more information on technical data collaboration maturity, the path manufacturers have followed to supplier collaboration success, and how to define your own path to supplier innovation, check out our eBook: The Technical Data Collaboration Maturity Model: Where Are You on the Path to a Next Generation Supplier Portal?